Understanding the Effects of Drive Train Misalignment on Bearing Fatigue Life
Improving the reliability of wind turbines is an essential component in the bid to minimise the cost of energy, especially for offshore wind due to the difficulties associated with access. Numerous studies have shown that wind turbine generator failure rates are unacceptably high, particularly given the long downtime incurred per failure. However, generator failures have, to date, received relatively little attention in the wind industry with the focus generally having been on the blades and the gearbox. There is evidence that the bearings are the most important source of generator failures; one important root cause of bearing failure is misalignment. An overview of publicly available wind turbine reliability data is presented in this article, and the importance of drive train misalignment is described.
By Matthew Whittle, University of Durham, UK
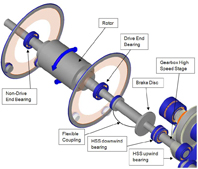
By Matthew Whittle, University of Durham, UK